Designing a mold for a complex solid shape such as a PVC pipe fitting is a complex task. Because of its complicated design and assembly, a plastic pipe fitting mold requires the skills of a highly skilled engineer. Typical designs require several parts, including two parts. Mold engineers with extensive experience in manufacturing PVC fittings should be hired to create molds. Here are some important considerations to keep in mind.
A proper mold for PVC pipe fittings is vital in reducing scrap. A well-designed mold can minimize scrap by making the runner as short as possible. This is also beneficial for reducing waste, since scraps are usually rejected parts. Besides, a well-made mold will be durable and long-lasting. For better performance, the PVC pipe fitting mould must be accurate and suitable for the purpose it was designed for.
The pipes and fittings industry is a global standard. An experienced PVC pipe fitting manufacturer can produce the same mold for multiple markets and products. Chemical and physical properties of PVC can be stressed when a mold is made. Injection molding is a time-consuming process, so it is imperative to be skilled in design and mold engineering. You will find that the results are well worth the extra time and effort. The benefits of PVC pipe fitting injection molding are numerous.
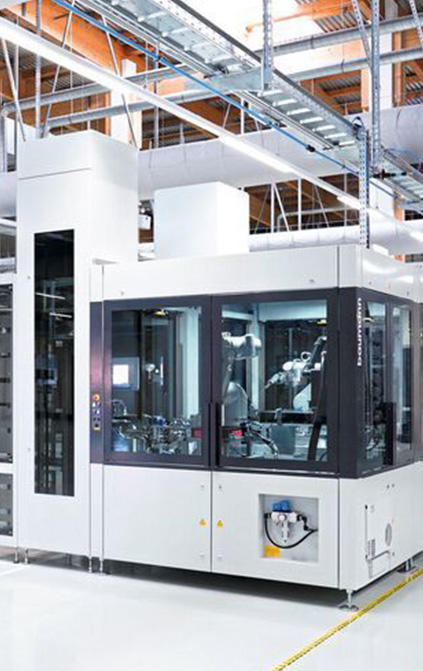