Injection molding is one of the fastest ways to produce plastic chairs. To manufacture a chair with this process, you need injection molding equipment, a material, and a mould. A plastic chair mould is made of PET, which has excellent mechanical properties and corrosion resistance. The plastic pellets are added to a hopper and heated to the desired melting point. They are then sent through an injection molding machine. The plastic pellets are then pressed into the mould. Once molded, the plastic chair is removed from the mould and cleaned by removing burrs.
Before buying a plastic chair mould, you must first determine the design of the chair. The mould needs to be created with proper measurement and analysis. It should meet the appearance and size requirements of the chair. The process also requires sophisticated mould making equipment and skilled workers. Because the process requires a complex plastic chair mould design, choosing a mould requires a thorough understanding of design, function, and previous similar chair designs. As the chair is an important part of a home, it's important to choose an appropriate mould for the job.
Plastic material is introduced into a mould cavity. The material is allowed to cool while the mold rotates. This ensures uniform cooling and prevents deformities. The part is then removed from the mold and is ready for use. The cooling process is a crucial part of the process, as it ensures that the plastic product retains its shape. And it requires a lot of time to cool. If you need a chair mould that is specifically designed for your needs, contact us today!
Injection moulding is a popular way to manufacture high volumes of plastic parts. This process is often used for surgical instruments and flexible products. However, the cost of the mould is high at first, as it requires high-strength steel or aluminium. However, as the volume of production increases, the price per unit decreases dramatically. The process itself can take up to four weeks, from tooling to production. It also requires high precision and is very time-consuming.
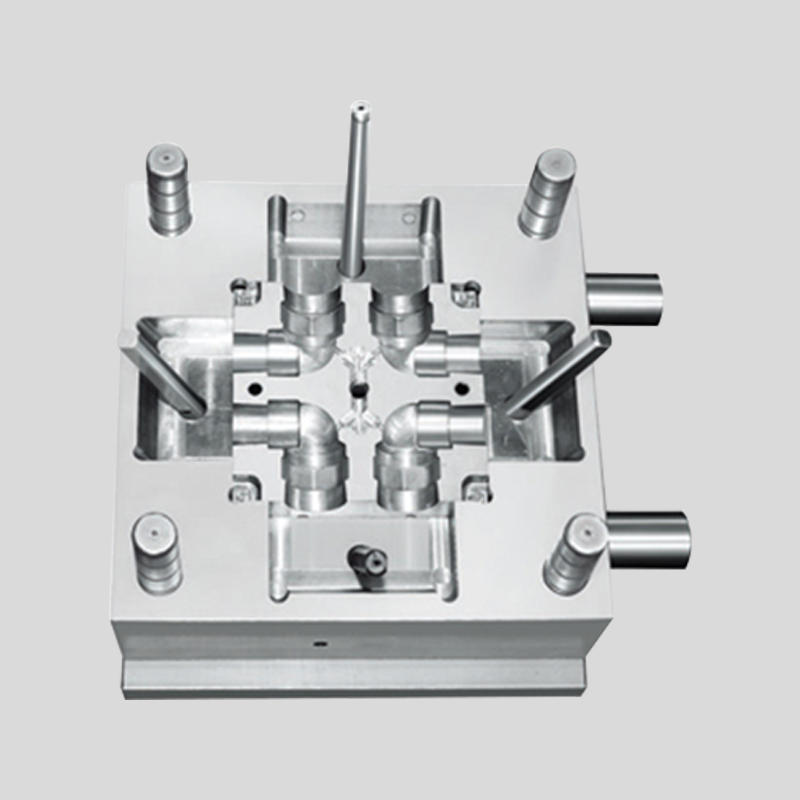